We may receive a commission when you use our affiliate links. However, this does not impact our recommendations.
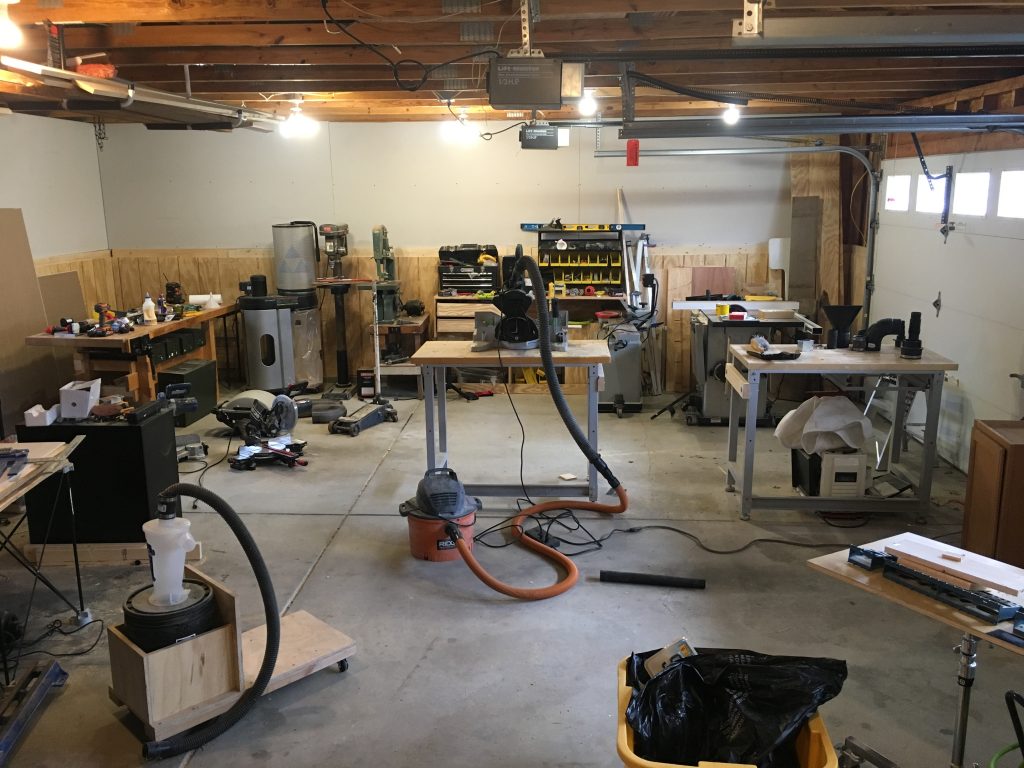
This is what the garage looked like after I had finally cleared all of the boxes and junk that landed here after the move that didn’t belong. I had already insulated and put up drywall on the far exterior wall.
A year and a half ago, I set up my home shop in somewhat of a hurry. For one, I was tired of not having a home shop and two, my proposal to build a shaker settee for the August issue was given the green light by my editor, Andrew Zoellner. So, my dad and I took spent a week transforming my unfinished two-car garage into a one-car garage with a one-car workshop.
We started by building a wall down the middle of the garage to give structure and boundaries to the workshop, my wife loves me, but not enough to give up parking in the garage. I know some folks make their shop mobile so they can move tables and machinery when the cars come in, but I’d rather have a smaller space that is dialed in and always ready to go. I have very little time to spend in the home shop. When I walk in, I have to make every minute count.
Anyway, once the shop was framed in and drywalled, we moved to lighting, running a subpanel and organizing the shop. With the shop set up enough to build my settee for the magazine, I got to work. I was kept warm during the build by a 230v heater that doubled my electric bill that month. But, the deadline was looming, so I took the hit and left insulating the ceiling for another day–it was almost summer anyway.
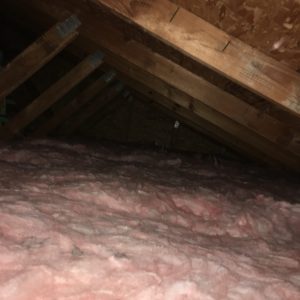
I used R-30 fiberglass insulation in the ceiling.
I’m not sure if this happened where you live, but we had about 48 hours of fall in Ohio. It went from 82deg one day, to 52deg the next and we just had our first frost. I’m looking forward to spending more and more time in the shop, but I don’t want to pay that crazy electric bill again. Last week I laid R-30 fiberglass batts on the ceiling of the shop and the walls have standard R-13. I’m hoping the ceiling was the major heat leak and this winter will be a bit more bearable.
Also, I am exploring flooring options. I know rubber mats are popular, have you put down foam or cork to keep the tootsies warm?
What are some of the best improvements you’ve made in your shop for dealing with the cold?
– David Lyell
Here are some supplies and tools we find essential in our everyday work around the shop. We may receive a commission from sales referred by our links; however, we have carefully selected these products for their usefulness and quality.
Living in southern Arizona presents the flip side of the winter problems but the solutions are mostly the same. A few years into retirement I sold my sporty car and used the proceeds to outfit a shop.
My current shop is half of a three-car garage with no dividers. The other half is occupied by an SUV and a golf cart. With summer temperatures averaging triple digits and the garage doors facing southwest, the shop was unusable from the first of May until sometime in October.
My solution was first to insulate. Garage doors were faced with fiberglass. Walls and ceiling were retrofitted with blown-in fiberglass. I built an insulated closet around the gas water heater to isolate the vent/combustion system. Also, partly for insulation and partly to save my tools from inevitable drops, I used an osb/foam product called Dri-core that was easy to install and added about R 1.5 to the floor. It supports the car easily as well.
Cooling the air was a must. I added a mini split unit air conditioner that also added some heat if needed during the winter. I found a model that was very DIY, needing no special tools to install. I really wanted to extract my sawdust from the shop by installing the dust collector outside, but I figured that would also extract all my cooled air in short order. I bit the bullet and opted for a hepa filter unit so the cool air circulates back into the shop.
Since I was essentially starting from scratch, I put in a subpanel and 240v wiring allowing my to install 240v tablesaw, bandsaw, jointer and the dust collector. All of this required pulling city permits and getting the required HOA permissions for the exterior AC, but that was a small hassle considering the alternative of non permitted work when selling a home–experience talking here.
I work slow. The whole thing came together in just a bit under a year, but it’s been worth it. I’m now finishing up on a split-top Roubo work bench as my first major project.
David,
Shop flooring has been covered by a most of the ww’ing mags…it depends on how much you’re willing to spend, and whether or not you have plans to use the garage for a car.
Vinyl mats (interlocking or sheet) are better than foam rubber placemats because they don’t catch dust or casters. They also provide a little protection from the cold, and soften the concrete.
A foam and plywood floor would offer even more comfort. In addition, the floor could serve as a workspace. (Scott Gibson wrote a story about this a few years back.)
If you add a floor, I second the vote for radiant heating. A small electric water heater might be enough to keep you warm enough, and avoid hassles of other heating options.
Good luck,
Joe
Congratulations on the new shop, David. I don’t think there’s anything more exciting than looking ahead planning the creating a new workshop.
My first shop was in a one car garage that I shared with my 1967 MGB GT. When I moved the car out to prep long stock, I had all of 240 square feet, so, the size of your space look luxurious. Heating and staying warm in the winter were serious challenges for me. Insulating and putting mats everywhere helped. Ideally, a suspended floor would be ideal in your case. There is a plastic panel system to suspend plywood flooring up off the concrete. I bought some but moved my shop before I had a chance to install it. Getting off the concrete makes all the difference.
After dealing with two shops with no built-in heating and cold concrete floors, I bit the bullet and desiged my current shop around hydronic heated floors.
Second recommendation. Think about woodworking tasks, moveable work stations and put everything in the shop on wheels. Even with a shop nearly 10 times the size of my first shop, I still keep everything moveable. Even my CNCs and on wheels. The only exception is my table saw, which after not moving it for 5 years, I sold the base.
Again, congrats!
Tim