We may receive a commission when you use our affiliate links. However, this does not impact our recommendations.
The furniture record shows us that “perfect dovetails” is a modern mania. As the photos of antiques above prove, even some of the ugliest joints will stay together for a very long time indeed (perhaps with a nail or two for good measure).
But James Krenov? He ruined us.
Nowadays, we strive for cutting perfect dovetails, right off the saw. So, how do you get there? Practice…lots of practice. And perhaps a few tricks.
So show me your best dovetail tricks – whether for hand-cut dovetails, power-tool-cut dovetails or a hybrid approach…and for through, half-blind, full-blind, mitered…all are welcome. If I get enough good ones (that we haven’t printed before), I’ll put together a “Tricks of the Trade” column for a future issue that features them. (And if we get only a handful of new-to-us clever tricks, I’ll print them in the regular Tricks columns – and, of course, pay the winners.)
Send those to me (with an image or two) – megan.fitzpatrick@fwmedia.com – with the subject line “Dovetail Trick” – and preferably before June 17, though we’re always looking for great tricks on any subject.
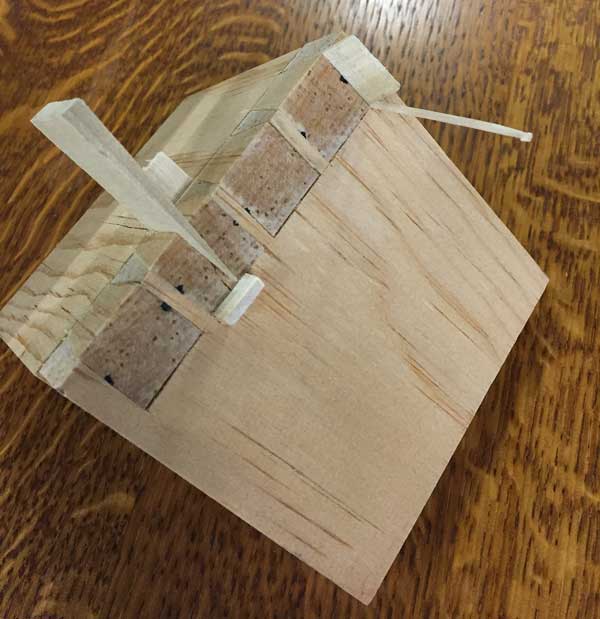
Porcupine tails? This gem has been kicking around in my car for a few months – left over from a talk I gave on “Light-tight dovetails: Fixes for Less-than-perfect Work.”
Here are some supplies and tools we find essential in our everyday work around the shop. We may receive a commission from sales referred by our links; however, we have carefully selected these products for their usefulness and quality.
What really changed dovetails for me was actually changing the saw I used. I had made a nice Tage Frid style bow saw, found it immensely useful, and then made another smaller bow saw with a fixed blade but with a very slight cant (about five degrees off of square). That very slight cant allowed me to tip the blade slightly off of the angle of the tail so that I could really see my work. Now I just cut all my right sided cuts, flip the work around and again cut on the right side. I pare the bottom of the tails slightly and then use a fret saw to cut out the waste.
I have always struggled with getting the perfect dove tail cut, tried various different techniques, even used guides. I think my lack of patients and heavy hands always get the better of me. I was asked by a friend of mine to build a lectern for his local community center and managed to make a right mess and ended up using these guys – Trade Cnc The guys at trade cnc advised to make my own jig from a template and have a go with the hand router.
The hardest thing for me has always been drawing a line around the board and have the lines meet. If they don’t meet you can’t make a set that will mesh without a gap. Only use the square from the side with your triangles marked on it.