We may receive a commission when you use our affiliate links. However, this does not impact our recommendations.
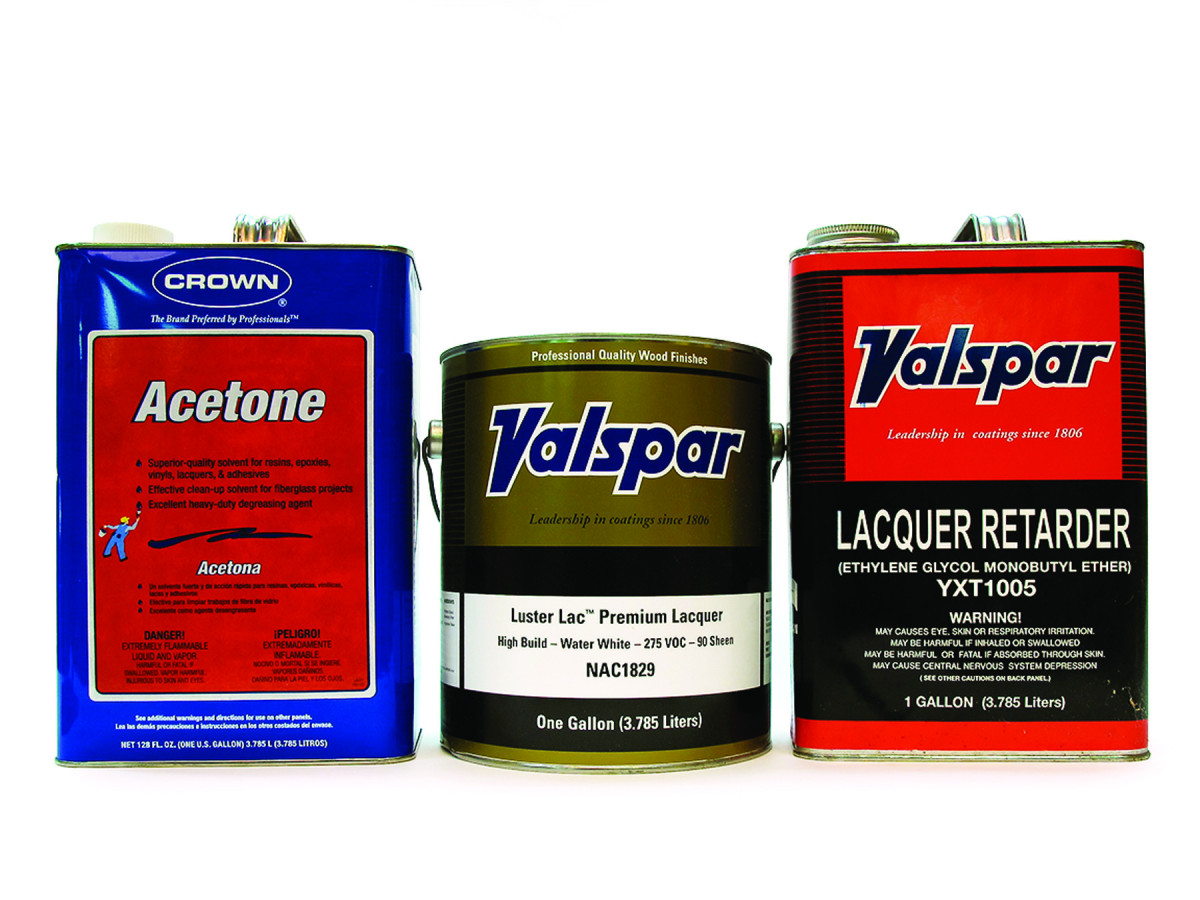
Compliant lacquers. Manufacturers make lacquer compliant with strict VOC laws, which usually limit non-exempt solvents to no more than 27.5 percent, by adding acetone, which is exempt. These lacquers dry fast and are usually labeled “275 VOC.” You can slow the drying by adding ethylene glycol monobutyl ether (butyl cellosolve) to the lacquer. Or you can add acetone to non-compliant lacquer to speed drying in cold temperatures.
This solvent’s versatility makes it ideal in many situations
If you’ve been shopping at paint stores or in the paint department of home centers for the last decade or so, you may have noticed the increased prominence of acetone among the solvents. There is a reason for this.
Acetone is among the very few solvents that have been exempted as a volatile organic compound (VOC) – an environmental (smog) pollutant. And it is the least expensive one, by far. Acetone is exempt because it has so little reactivity.
Being exempt means there are no regulatory restrictions on how much of this solvent we, or the manufacturers we buy from, use. No other commonly available solvent, except water, is so free of restrictions.
Moreover, though acetone has a noticeable odor (which makes it seem toxic), it is actually a fairly benign solvent in vapor form, limited at low exposure to causing only mild irritation of the central nervous system.
Acetone is especially useful because it is miscible with all common solvents and water, and thus most common paints, finishes and coloring products. So acetone can be added in significant percentages to most coating materials.
Also important, acetone is the fastest evaporating and one of the strongest of all commonly available solvents, and it is very dry (meaning non-oily). So it makes an excellent cleaner and degreaser and this is how it is used in most other industries.
The fast evaporation corresponds, however, to high flammability. A flame or spark can set off an explosion or flash fire if vapors build up enough. You should always work with a good exhaust system if you are using the solvent in significant quantities.
The strength means that acetone can damage or remove most paints and finishes, so you should avoid using this solvent as a cleaner on all but the most solvent-resistant finishes. These include conversion varnish, two-part polyurethane, UV-cured finish and epoxy resin. On oil-based polyurethane, test first and be sparing in your use.
Formulating
Because acetone is an exempt solvent, finish manufacturers can include as much as they want in their products. This is significant because it makes possible the continued availability of many products, especially lacquers and non-grain raising (NGR) dye stains that would otherwise be taken off the market in areas with strict environmental laws.
For example, lacquers require a great deal of solvent (often 75 percent or more) to be sprayable, and NGR dye stains, which used to contain methanol, are entirely solvent. Many areas, including California, limit VOC content in lacquer to as low as 27.5 percent, (275 grams/liter). So there would be no way, or at least no inexpensive way, for lacquers and dye stains to comply if it weren’t for acetone.
While this is good for us because it keeps products we use on the market, it changes the application characteristics significantly. Any finishing product that contains a large amount of acetone dries very rapidly.
Fast drying can cause dry spray and blushing (the finish turns milky white) in finishes and toners. It can also cause an NGR dye stain to dry so fast that it doesn’t wet the wood enough to bring out the expected color.
You can overcome the often too-fast drying by adding some very slow evaporating butyl cellosolve (also labeled Super Retarder, EB, 2-butoxyethanol or ethylene glycol monobutyl ether), which is widely available from distributors and paint stores that sell to the trade. Be aware, however, that adding anything to the product could take it out of compliance in some areas.
Drying
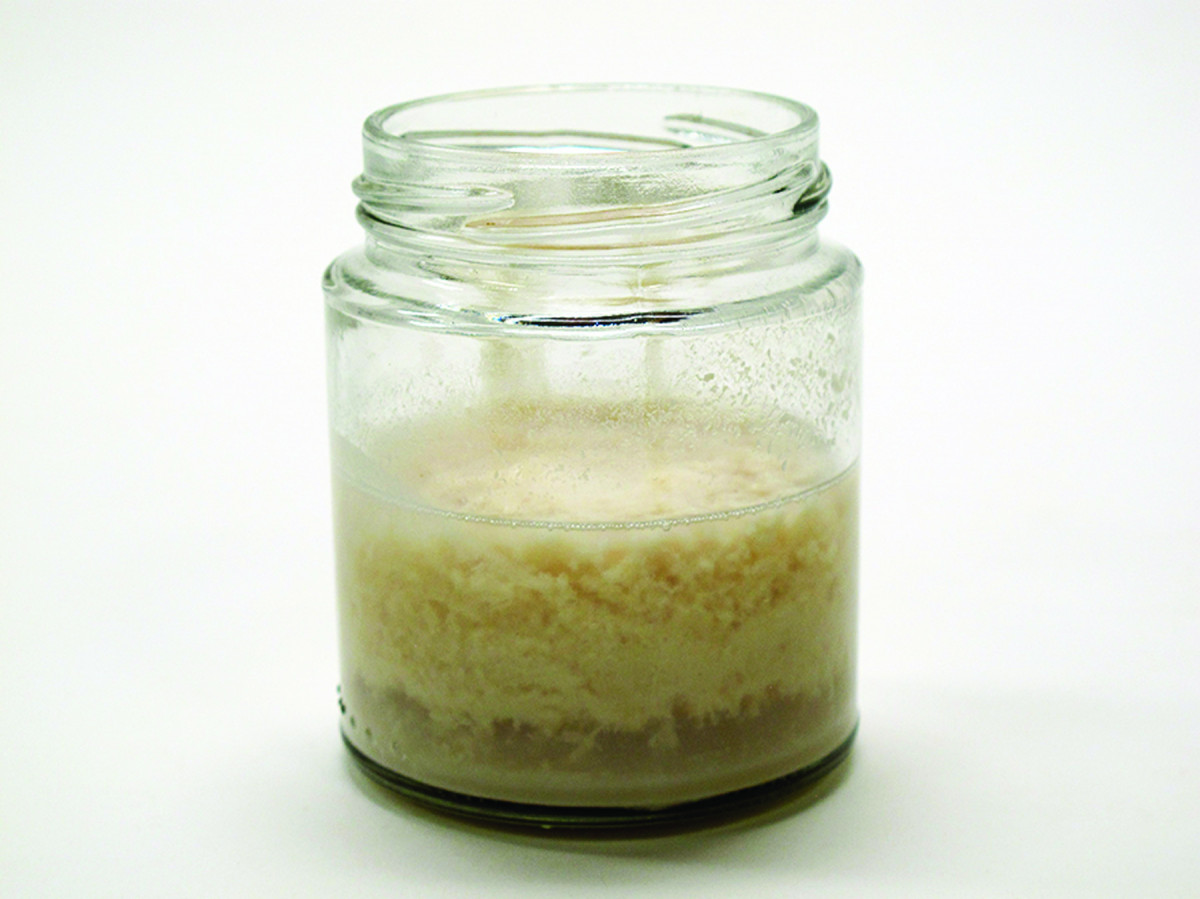
Thinning with acetone. You can thin most finishes with acetone, but test water-based finishes first because some, like the one pictured here, coagulate. Most that I’ve tested don’t have this problem.
The fast evaporation rate of acetone can be very helpful in cold temperatures when everything dries slower.
Because acetone is compatible or mixable with most finishes and stains, you can add the solvent to speed drying. Acetone is especially effective with shellac and every type of lacquer. Some water-based finishes, however, coagulate when acetone is added. You should test first in a small jar.
Adding acetone to varnish, oil stains or glazes has less effect on the drying because these products cure primarily by the absorption of oxygen, not by solvent evaporation. The tacky stage may be reached more quickly, but the product still has to go through the longer oxidation process.
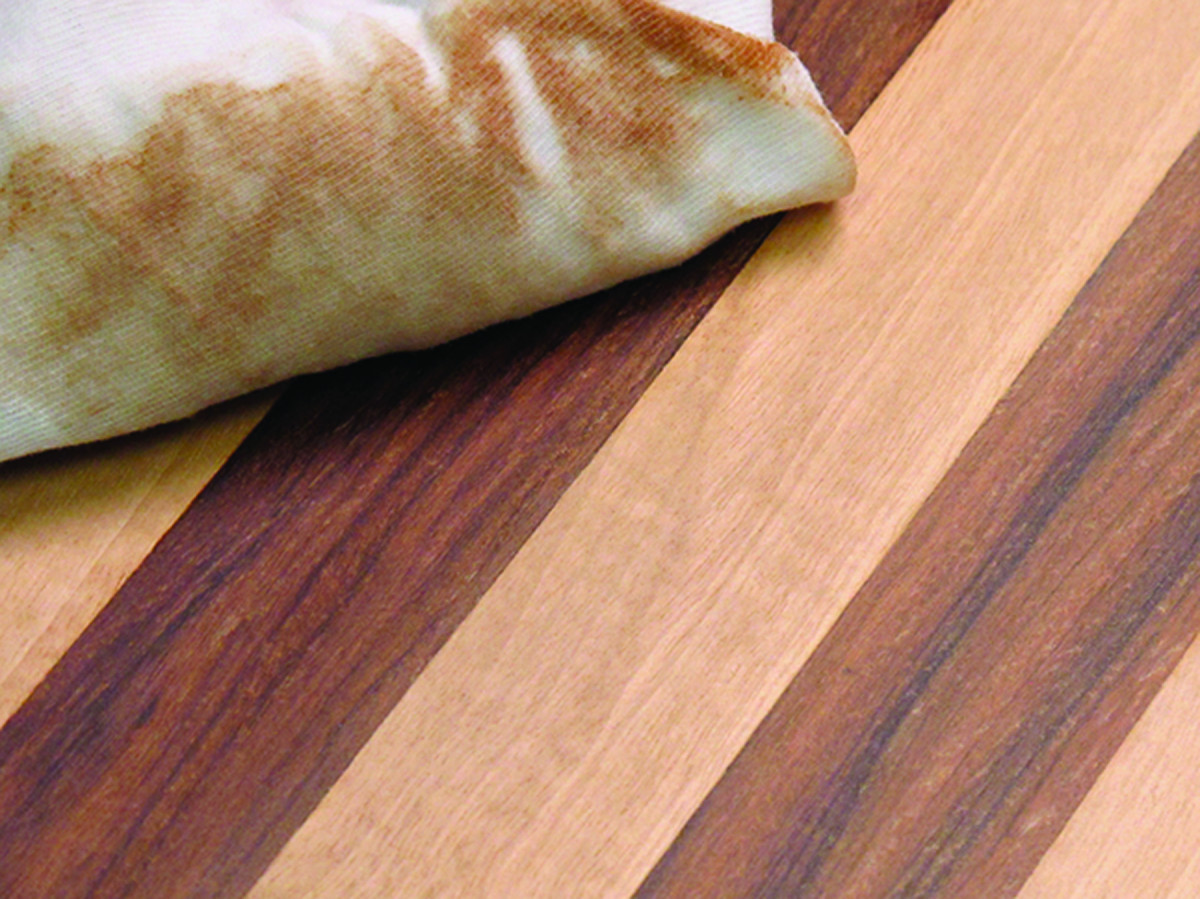
Removing oily resin. Acetone is great for removing the oily resin from exotic woods before gluing or finishing. But be careful if several woods are mixed. The solvent can pick up some of the color from the darker woods and transfer it to the lighter woods.
Keep in mind that thinning any product results in less build, so you may need to apply more coats.
Cleaning
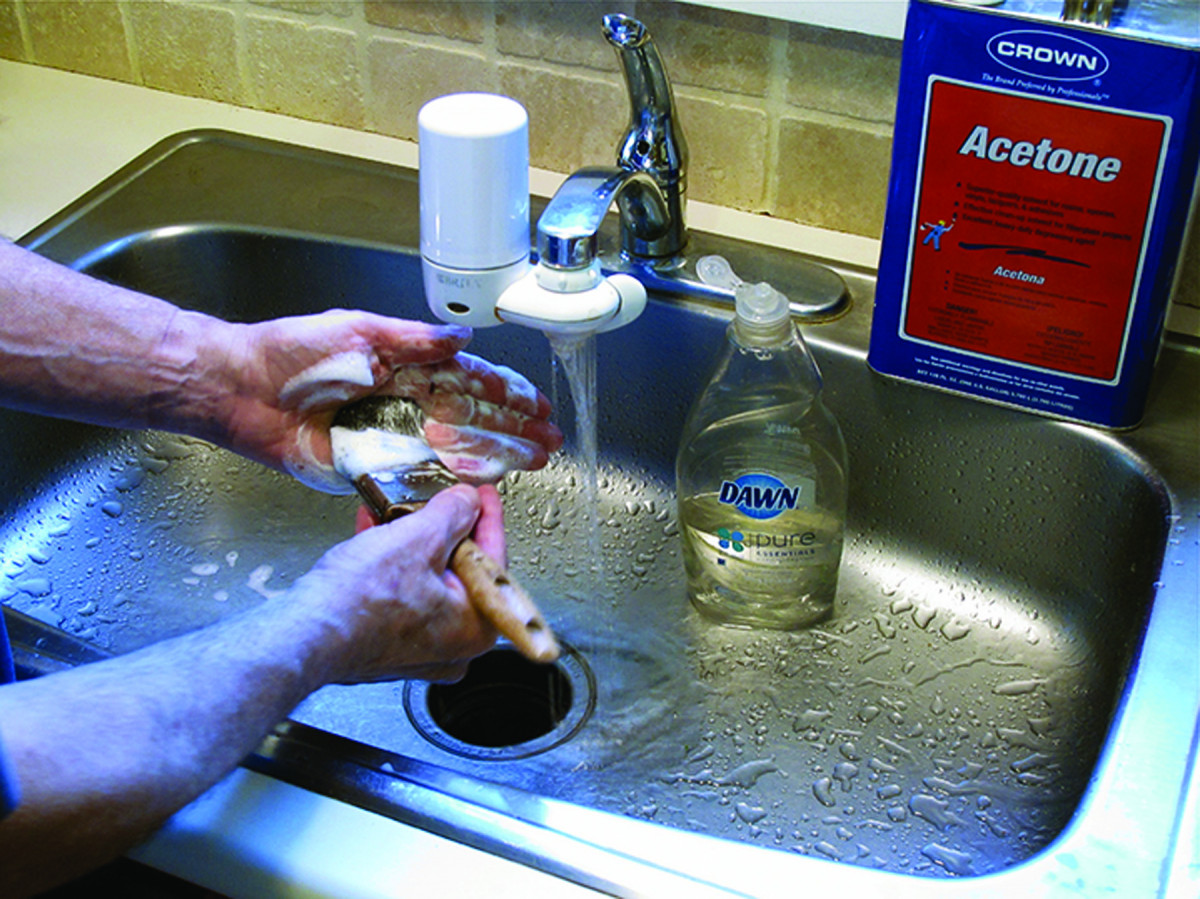
Cleaning brushes. Many woodworkers use cheap throwaway brushes for varnish and polyurethane because brushes are so hard to clean. Washing with soap and water is much easier if you rinse the brush in acetone after a first rinse in mineral spirits. Suds like these, which indicate the brush is clean, usually appear in the first washing.
Acetone is commonly used as a cleaner and degreaser in labs and in industry. It is also used as the active ingredient in fingernail polish removers and as the solvent for removing epoxy and cyanoacrylate adhesives such as Super Glue from hands or other surfaces before the adhesive hardens.
More specific to finishing, acetone is the best cleaner for removing the resinous oils in exotic woods such as teak, rosewood and cocobolo – much more effective than naphtha or denatured alcohol. These oils can weaken the bond of water-based adhesives and finishes, and significantly slow the drying of oil and varnish finishes.
To improve the bonding or drying speed, wipe the surface of the wood with acetone just before applying the glue or finish.
Because acetone is miscible with water, it’s also useful for removing residue water from spray equipment when switching from a water-based to a solvent-based product.
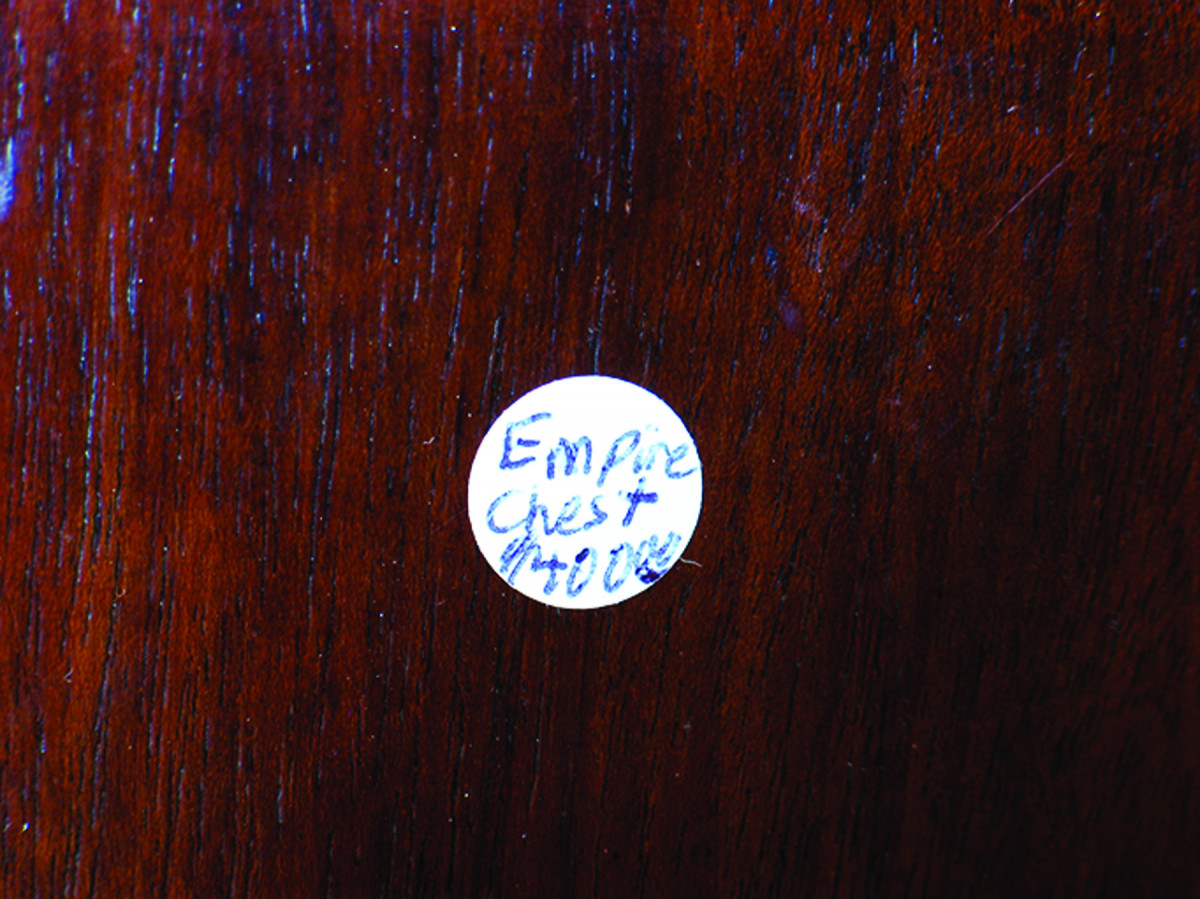
Stuck stickers & tape. Stickers and tape can become so stuck to a surface that you can’t peel them off. Wiping with an acetone-wetted cloth usually makes removal easy, but first try a milder solvent such as naphtha on most finishes because acetone will damage them.
And because acetone is miscible with mineral spirits, it’s useful for speeding the cleaning of varnish, oil-stain and oil-glaze brushes after the mineral-spirits rinse, but before washing in soap and water. It’s the residue from mineral spirits that makes washing so time-consuming, because of the number of washings necessary to remove it.
Of course, acetone is excellent for cleaning spray guns used for spraying any finishing product.
Acetone’s solvent strength makes it the most effective solvent for removing masking tape and stickers that have been stuck to a surface for so long they no longer peel off. But the solvent may also damage or remove a finish, so it’s usually best to try weaker denatured alcohol or naphtha first.
The solvent strength makes acetone excellent for removing paints and finishes, so it is a common ingredient in paint and varnish removers. Evaporation is retarded by the inclusion of paraffin wax, which rises to the surface of thickly applied remover and forms a barrier.
Bob is author of “Flexner on Finishing,” “Wood Finishing 101” and “Understanding Wood Finishing.”
Here are some supplies and tools we find essential in our everyday work around the shop. We may receive a commission from sales referred by our links; however, we have carefully selected these products for their usefulness and quality.