We may receive a commission when you use our affiliate links. However, this does not impact our recommendations.
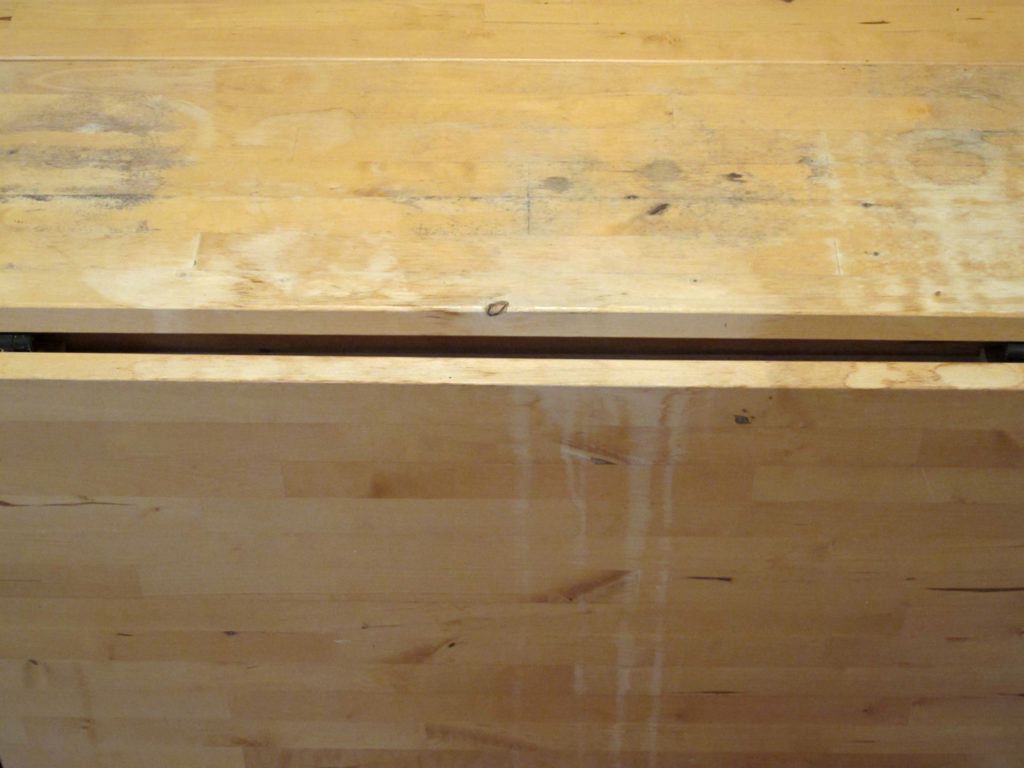
My wife uses this drop-leaf table from Ikea with the leaves down for her potted plants. The catalyzed finish is too thin to be very functional.
I’ve written this many times and said it many more. The film thickness of a finish is much more important for preventing water getting through to the wood than the type of finish. For example, polyurethane is more water resistant than shellac. But three coats of shellac is much more water resistant than one coat of wipe-on polyurethane.
It makes sense if you think about it.
Likewise, an oil finish, which doesn’t harden well, so it can’t be built up, is almost worthless for water resistance. This is true despite the absurd claim from some companies that the oil protects the wood from the inside.
The drop-leaf table pictured here provides a great example of the importance of film thickness. It’s from Ikea and made in Europe, probably in Sweden or Poland. The finish on it is very thin. It didn’t take long for the center part to be damaged by water as the table sits on our covered deck with the drop leaves down and serves largely as a resting place for my wife’s potted plants. This despite the finish being a very durable and protective catalyzed lacquer or catalyzed varnish.
How do I know what finish was used? Partly because I know that catalyzed finishes are very popular in factories in northern Europe and partly because of a very simple test I performed. I dabbed on some lacquer thinner with my finger to see if the finish would get sticky or soft. It didn’t. It wasn’t sticky and I wasn’t able to scrape away any of it with my fingernail. This told me that the finish wasn’t nitrocellulose lacquer or water-based finish because the lacquer thinner would have softened these finishes and made them sticky.
So the finish had to be something else. Because the table was made in a factory the finish must have been sprayed and must be fast drying. No factory would mess with varnish or polyurethane because these take too long to dry, slowing production unacceptably. And no factories use shellac. That leaves for sure a high-performance finish and almost for sure a catalyzed finish.
Catalyzed finishes are at least as water resistant as polyurethane. Typically with Ikea finishes, these catalyzed finishes are sprayed very thin, and this is the problem with this table. It did, however, give me a great example of the importance of thickness (or lack thereof) for water resistance.
– Bob Flexner
Here are some supplies and tools we find essential in our everyday work around the shop. We may receive a commission from sales referred by our links; however, we have carefully selected these products for their usefulness and quality.
In all the wood finishing books and articles, I have never heard this. I find this very helpful, and to be honest, liberating. Thanks again Bob for your clarity, and insightful blogs.
I have not written about these finishes. I’ve felt about them as you do. But I’ve now been asked about them several times so I guess I need to do a little testing.
Hi, I found your article very useful. Does it matter the kind of wood to be used when you talk about finishing wood furnish?
As you probably know, “hardwax oils” are becoming very popular with woodworkers. I am not sure if you have written about these products (such as Osmo Polyx, Rubio Monocoat, Fiddes). They are popular “green” floor finishes and are making their way into the woodworker market. I mention it because they promise to be water resistant, which is hard to believe for such an in the wood looking finish. My guess is they perform a lot like an oil/varnish blend (only partially cure, with a similar level of protection), with the added benefit of costing more!
If you have not written about them, an article demystifying them would be interesting. Although they are marketed as plant based products, Osmo’s safety data sheet lists petroleum distillates, paraffin wax and dryers (making more like a ‘traditional’ finish than people realize).