We may receive a commission when you use our affiliate links. However, this does not impact our recommendations.
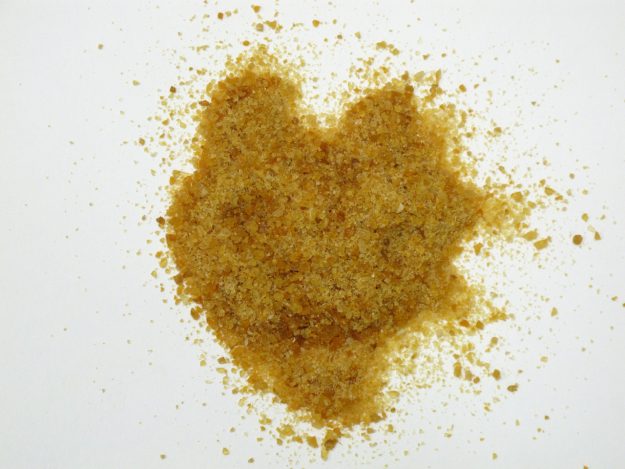
192 gram-strength hide glue
The largest, and I think only, hide-glue factory left in the United States is Milligan & Higgins, located in Johnstown, New York, west of Albany, off Interstate 90. You can buy hide glue directly from the company in 50-pound or larger quantities.
For smaller quantities, resellers include Woodworker’s Supply, Tools for Working Wood, Merit Industries/Wood Finish Supply and a number of suppliers to the musical-instrument industry.
My experience with hide glue from sources other than Milligan & Higgins is that the glue stinks considerably more. The explanation from Milligan & Higgins is that they take pains to remove more of the bacteria that cause the bad smell.
So here’s how Milligan & Higgins makes the glue (I visited in the 1990s to actually see the process).
First, trimmings from cowhides taken from a nearby tannery are washed then treated with lime many times in large vats that look like freight cars with open tops. This goes on for one to three months.
The limed skins are then washed and neutralized with dilute acid. Washing with water many times then removes the lime, salts and the acid.
The skin stock is then transferred to kettles and heated with hot water. This removes the collagen – the fibrous, albumin-like material found in the skin and connective tissues of animals. (Hooves and horns don’t contain collagen and aren’t used, contrary to what you often hear.) Successive extractions of glue are made, with these being designated “first run,” “second run,” etc. In general, glue made from the early extractions excels later extractions in gel strength and clear color.
The dilute solution from the hot water is filtered and evaporated to about 40% concentration. Then the solution is chilled and pushed through a large plate with small holes similar to a giant pasta machine to form “noodles.” The noodles are then dried further on a conveyer to keep them apart so they don’t stick to each other.
The final step is to break the noodles into pieces, which are ground and stored in large bins to be blended later. The blends are graded by “gram strength” from a high of 512 grams to a low of 85 grams.
The higher the gram strength the stronger the glue, but the faster it gels. So higher gram strengths are unworkable in woodworking because they gel too fast. But lower gram strengths are still plenty strong to make a bond stronger than the wood.
The gram strength I’ve used for 40 years is 192-gram strength (on the recommendation of Milligan & Higgins). But 222 or 251 are often used by musical instrument makers (for whatever reason I don’t know; maybe because they are working on smaller objects; or maybe because this is just what they got started with and are used to).
Looking around on the Internet I found a very interesting video of a fellow making his own glue from hides. The video creator follows roughly the same process I’ve described. If you’re interested, I highly recommend it.
— Bob Flexner
Here are some supplies and tools we find essential in our everyday work around the shop. We may receive a commission from sales referred by our links; however, we have carefully selected these products for their usefulness and quality.